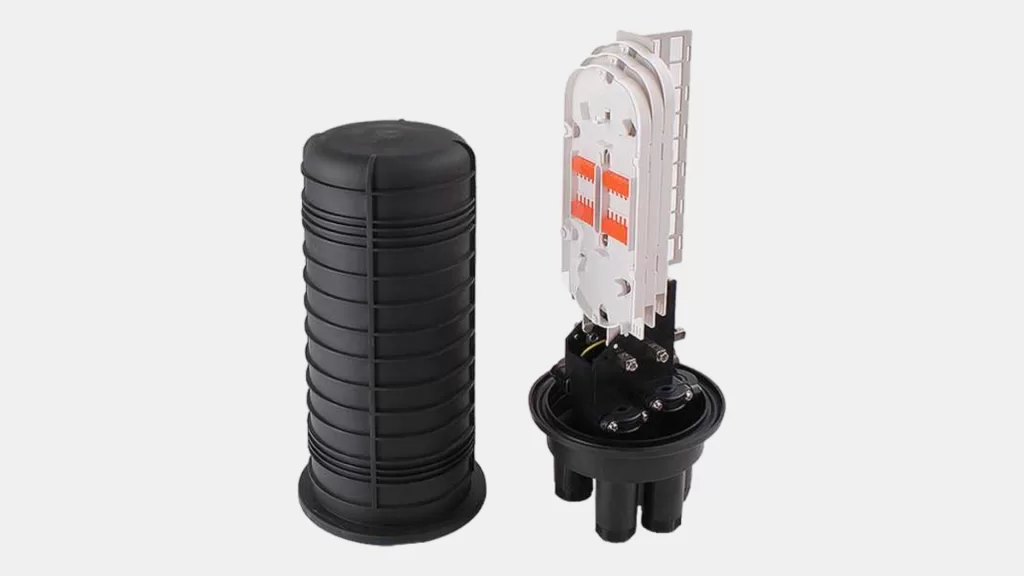
The fiber optic splice closure is an important tool for splicing optical cables. Its material selection and construction are crucial to ensuring the transmission performance and service life of the optical cable. This article will discuss in detail the material selection principles of optical cable splice boxes and precautions during the construction process, aiming to provide useful reference for relevant engineering personnel.
Material selection for fiber optic splice closures
The fiber optic splice closure is a closed structure used for splicing, protecting and managing optical fibers. Its material selection is crucial to ensure the quality and service life of the fiber optic splice closure. The following is a detailed introduction to the selection of materials for fiber optic splice closures:
High-quality engineering plastics: The outer shell and internal structural parts of the fiber optic splice closure are usually made of high-quality engineering plastics, such as ABS, PC, etc. These materials have high strength, corrosion resistance, aging resistance, impact resistance and other characteristics, and can ensure the mechanical properties and stability of the fiber optic splice closure.
High-strength aluminum alloy: In order to meet the needs of some special occasions, such as outdoor use or when carrying larger loads, fiber optic splice closures can be made of high-strength aluminum alloy materials. Aluminum alloy has the advantages of lightness, corrosion resistance, and high strength, which can ensure the durability and reliability of the fiber optic splice closure.
Sealing material: In order to ensure the waterproof and dustproof performance of the fiber optic splice closure, the selection of sealing material is also very important. Commonly used sealing materials include rubber, silicone, etc., which have good elasticity and durability and can effectively prevent moisture, dust, etc. from entering the inside of the fiber optic splice closure.
Insulating materials: Inside the fiber optic splice closure, insulating materials are needed to ensure the isolation of optical fibers and electrical signals. Common insulation materials include PC, PVC, etc., which have good insulation properties and high temperature resistance, and can ensure the safety and stability of the fiber optic splice closure during use.
Precautions for construction of fiber optic splice closures
The construction quality and maintenance of fiber optic splice closures are of great significance to ensure the normal operation and service life of fiber optic lines. The following are the things you need to pay attention to when constructing fiber optic splice closures:
Pre-construction preparation: Before constructing the fiber optic splice closure, it is necessary to fully understand the routing and laying methods of optical fiber lines, and prepare the required optical fibers, connectors, adapters and other materials and tools. At the same time, it is necessary to ensure that the construction environment is clean and tidy to avoid dust, moisture and other factors from affecting the construction quality.
Clean the optical fiber: Before splicing the optical fiber, the optical fiber needs to be thoroughly cleaned to remove dirt and impurities on its surface. When cleaning, pay attention to using the correct cleaning agent and cleaning method to avoid damage or contamination of the optical fiber.
Correctly install the connector: When inserting the optical fiber connector into the fiber optic splice closure, make sure the end face of the connector is flat and free of impurities to avoid jamming or damage during insertion. At the same time, ensure that the connector model and specifications match the fiber optic splice closure to avoid incompatibility.
Fixing the optical fiber: When placing the optical fiber into the fiber optic splice closure, make sure that the optical fiber is firmly fixed in the closure to avoid shaking or shifting during construction or use. The optical fiber can be fixed using special optical fiber clamps or tape.
Sealed fiber optic splice closure: After completing the optical fiber splice, the fiber optic splice closure must be sealed to prevent dust, moisture, etc. from entering the closure and affecting the optical fiber. When sealing, appropriate sealing materials and methods should be selected to ensure good sealing effect and no damage to the closure body.
Marking and identification: After completing the construction of the fiber optic splice closure, each connector must be marked and identified to facilitate future maintenance and management. The markings should be clear and accurate so that the purpose and attributes of each connector can be quickly identified.
Regular maintenance: In order to ensure the normal use and extend the service life of the fiber optic splice closure, it needs to be maintained regularly. Including checking whether the seal is good, cleaning up dust, checking whether there are any abnormalities in the optical fiber, etc. Problems found must be dealt with promptly to avoid affecting the normal operation of the entire optical fiber line.
Conclusion
When selecting and using fiber optic splice closures, we must pay attention to the quality and performance of the materials. At the same time, we must pay attention to the control of every detail during the construction process to ensure that the construction quality and use effect are optimal. At the same time, later maintenance and management are also important links to ensure the long-term stable operation of the fiber optic splice closure.