Innerduct, a protective pathway for cables within conduits, comes in two main forms: rigid and textile. While both serve the purpose of cable protection, their properties and applications differ significantly. We will explore the advantages and disadvantages of each type, ultimately highlighting why textile innerduct emerges as the superior choice for modern installations.
Rigid Innerduct: Traditional, But Limited
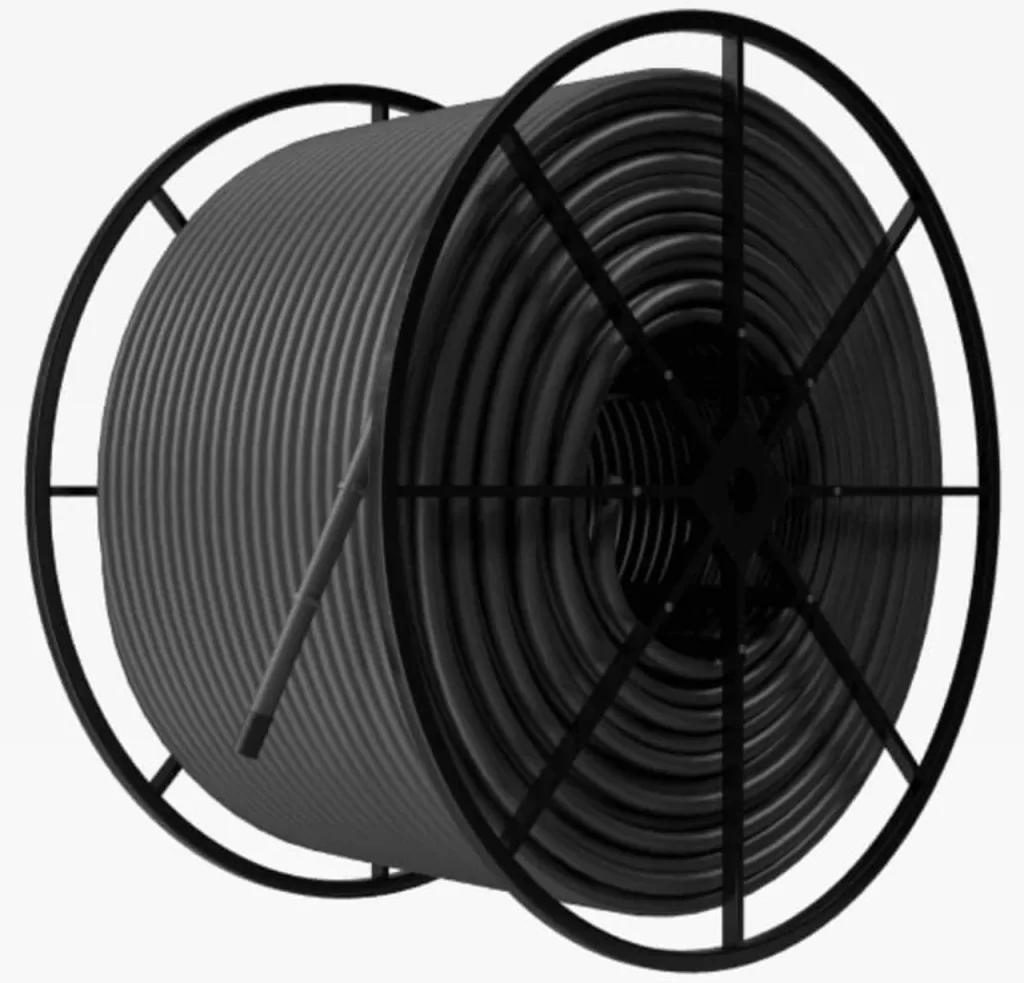
Rigid innerduct, typically made from High-Density Polyethylene (HDPE), offers a strong and stable enclosure for cables.
Pros:
- Durability: HDPE is resistant to impact, chemicals, and corrosion.
- Fire Resistance: Certain formulations of HDPE offer fire-retardant properties.
Cons:
- Limited Flexibility: Rigid innerduct requires straight runs and large bending radii, making installation in tight spaces difficult.
- Increased Installation Time: Rigid innerduct often requires more planning and pre-work to ensure proper routing.
- Reduced Capacity: Rigid innerduct typically houses only one cable, requiring additional conduits for multiple cables.
- Higher Pulling Tension: Friction between the cable and the smooth inner wall of rigid innerduct can increase pulling tension during installation.
Rigid Innerduct Applications:
- Suitable for exposed runs where strength and fire resistance are priorities.
- Can be used for short underground installations with ample space.
Textile Innerduct: Flexible and Future-Proof
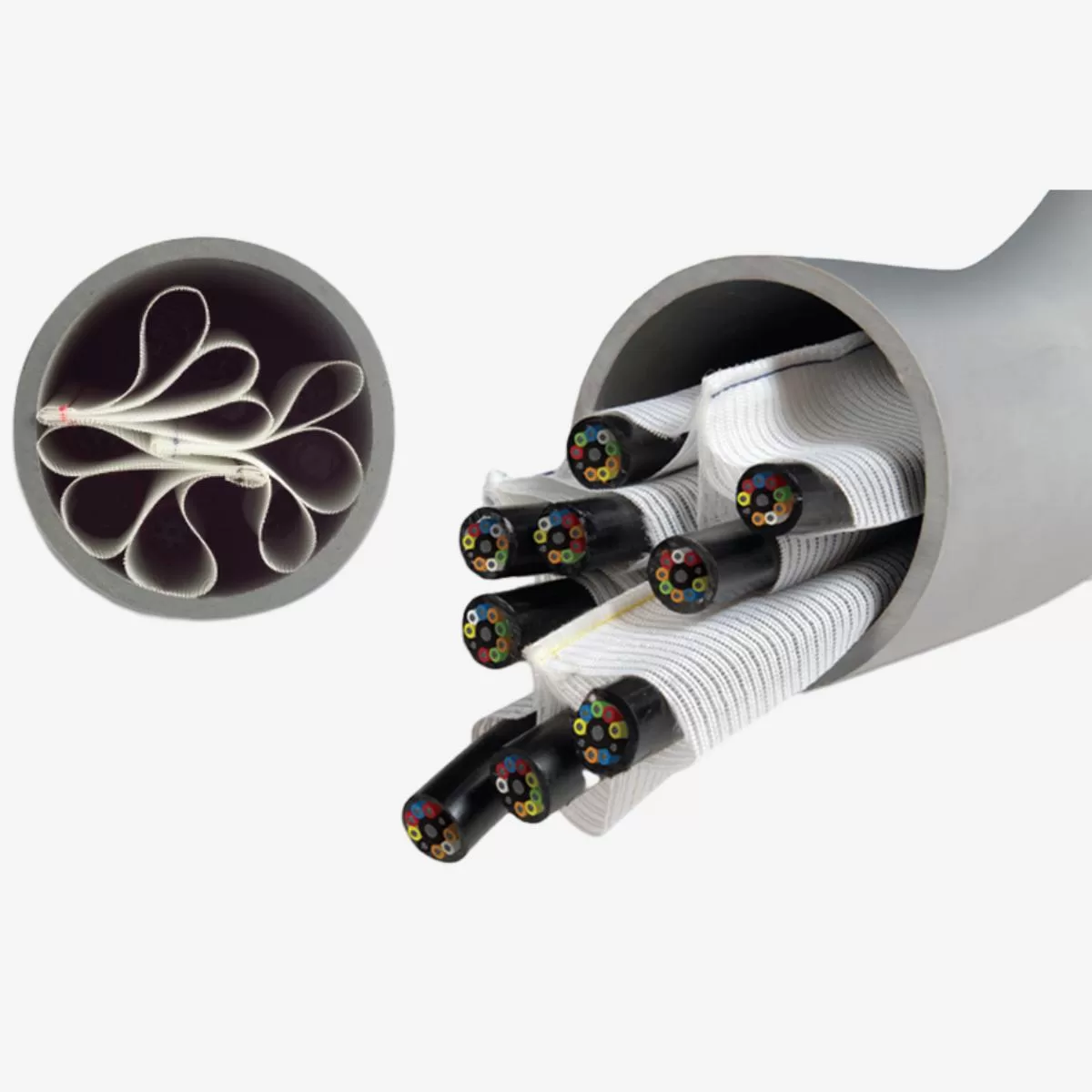
Textile innerduct, constructed from woven polyester filaments, offers a unique combination of flexibility and strength.
Pros:
- Superior Flexibility: Textile innerduct bends easily, allowing for installation in tight spaces and around corners.
- Reduced Installation Time: Flexible layouts are achievable, minimizing pre-work and simplifying installation.
- Increased Capacity: Multi-cell configurations allow housing multiple cables within a single innerduct, reducing conduit needs.
- Lower Pulling Tension: The textured surface of textile innerduct reduces friction, making cable pulling easier.
- Future-Proofing: Additional cables can be easily added to existing textile innerduct systems as network demands grow.
Cons:
- Slightly Lower Crush Resistance: Compared to rigid HDPE, textile innerduct may offer slightly less crush protection.
Textile Innerduct Applications:
- Ideal for congested areas, under raised floors, and in-building applications.
- Well-suited for long underground installations and retrofitting existing conduit systems.
- Perfect for data centers and other environments where future cable additions are anticipated.
Comparison of Key Properties
Feature | Rigid Innerduct | Textile Innerduct |
---|---|---|
Material | HDPE | Polyester Filaments |
Flexibility | Low | High |
Ease of Installation | Difficult | Easy |
Cable Capacity | Single | Multiple (Multi-cell) |
Pulling Tension | High | High |
Future-Proofing | Limited | Excellent |
Textile Innerduct: The Clear Choice
While rigid innerduct has its place in specific applications, textile innerduct offers significant advantages for most modern installations. Its flexibility simplifies installation, reduces costs, and allows for future network expansion. Additionally, the lower pulling tension of textile innerduct protects cables from damage during installation.
The Future is Flexible
As data needs continue to grow, the ability to easily add cables to existing infrastructure becomes ever more critical. Textile innerduct, with its inherent flexibility and future-proofing capabilities, positions itself as the clear choice for a wide range of applications.